In our investment casting parts, various quality control measures are employed to ensure the production of high-quality components. These measures include:
Visual Inspection: Visual inspection is conducted to detect any visible defects such as surface irregularities, bend, cracks, or porosity. Our trained inspectors carefully examine the cast parts to identify any issues that may affect the quality or functionality of the parts.
Dimensional Inspection: Dimensional inspection involves measuring critical dimensions and tolerances of the investment cast parts. This is typically done using precision instruments such as calipers, micrometers, coordinate measuring machines (CMM), or optical measurement systems. The measurements are compared against the required specifications to ensure that the parts meet the dimensional requirements.
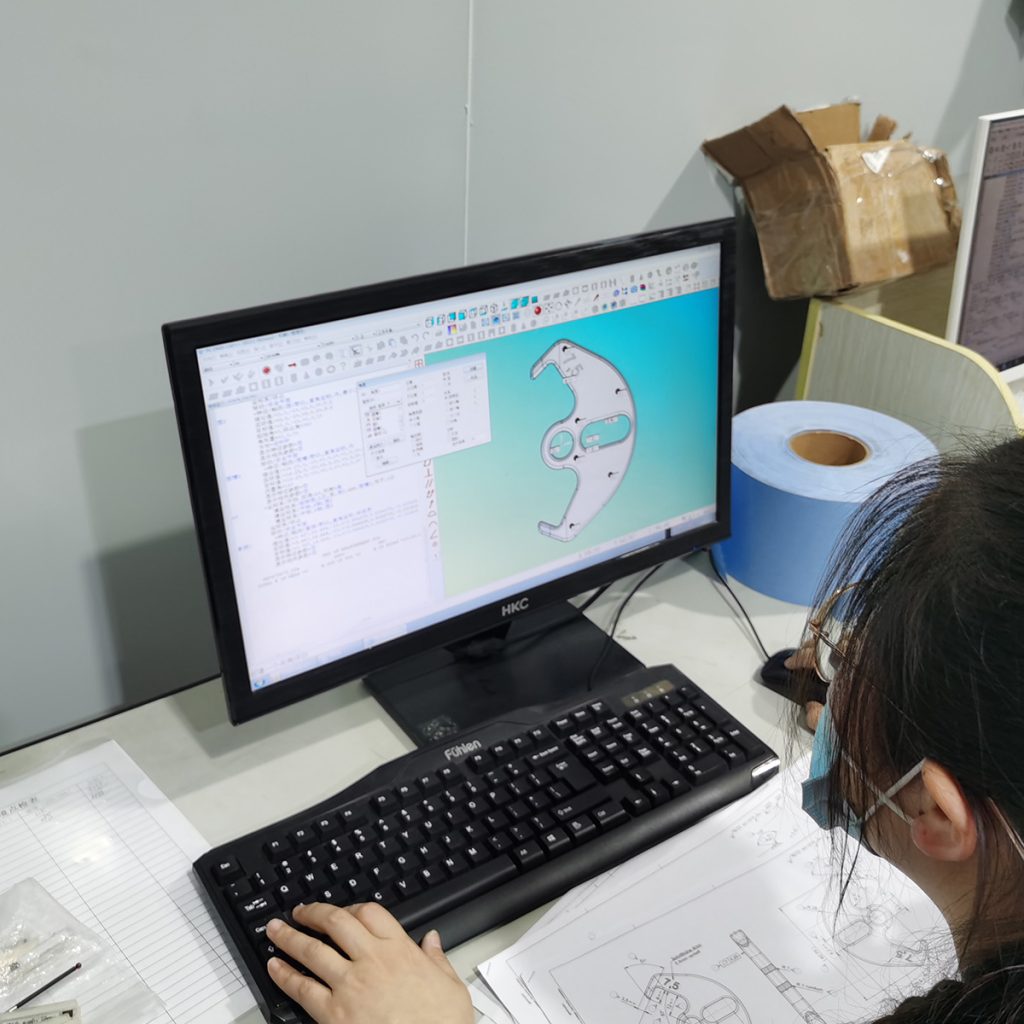
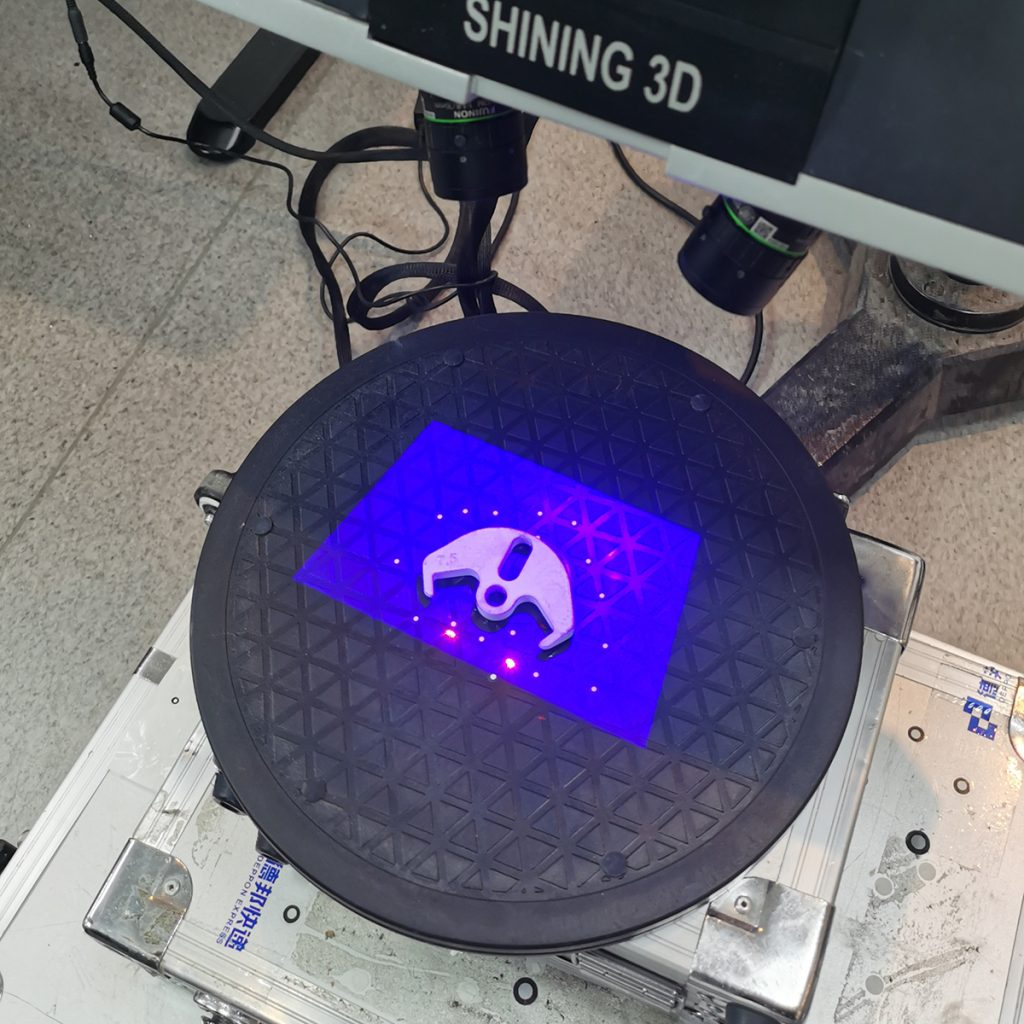
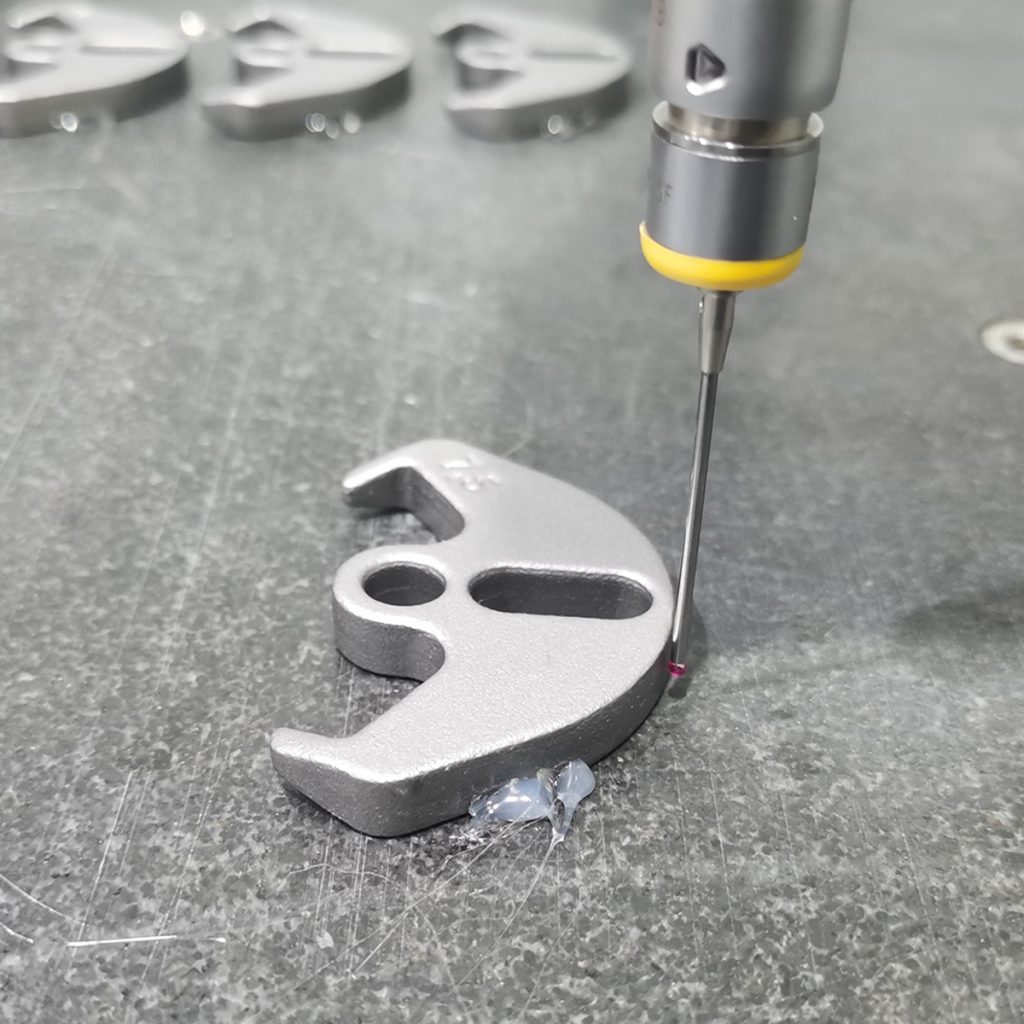
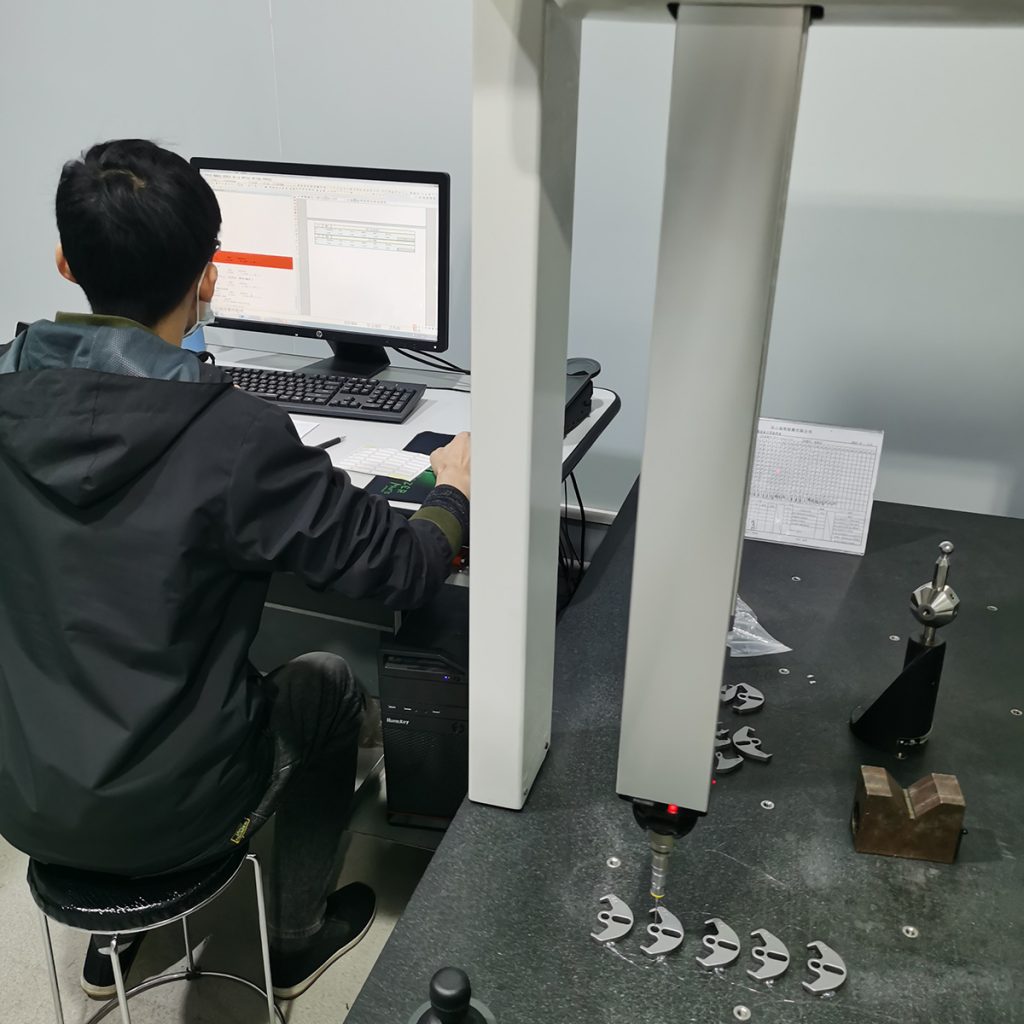
Non-Destructive Testing (NDT): Non-destructive testing techniques are employed to identify internal defects or anomalies without causing damage to the cast parts. Common NDT methods used in investment casting include X-ray inspection, ultrasonic testing, magnetic particle testing, and dye penetrant inspection. These methods can detect defects such as cracks, voids, inclusions, or discontinuities that may be hidden from visual inspection.
Mechanical Testing: Mechanical testing is performed to assess the mechanical properties and performance of the investment cast parts. This may include tests such as tensile testing, hardness testing, impact testing, or fatigue testing. By subjecting the parts to controlled forces or stresses, their strength, ductility, and other mechanical characteristics can be evaluated to ensure they meet the required standards.
Chemical Analysis: Chemical analysis is carried out to verify the composition of the cast parts. It ensures that the material used for casting matches the specified chemical composition, which is crucial for meeting the desired mechanical properties and performance requirements.
Surface Finish Inspection: The surface finish of investment cast parts is inspected to ensure it meets the required specifications. Surface roughness, burrs, flash, or other surface imperfections are assessed and addressed if necessary.
Heat Treatment Verification: If heat treatment is performed on the investment cast parts to enhance their mechanical properties, the heat treatment process is verified to ensure proper temperature, time, and cooling methods were followed. This helps ensure that the parts achieve the desired material properties.
Documentation and Traceability: Thorough documentation is maintained throughout the quality control process, including inspection reports, test results, certificates of conformity, and traceability records. This enables the tracking and verification of each component’s quality and allows for effective quality control and management.
By implementing these quality control measures, investment casting parts can be thoroughly inspected and tested to ensure they meet the required specifications, performance standards, and customer expectations.